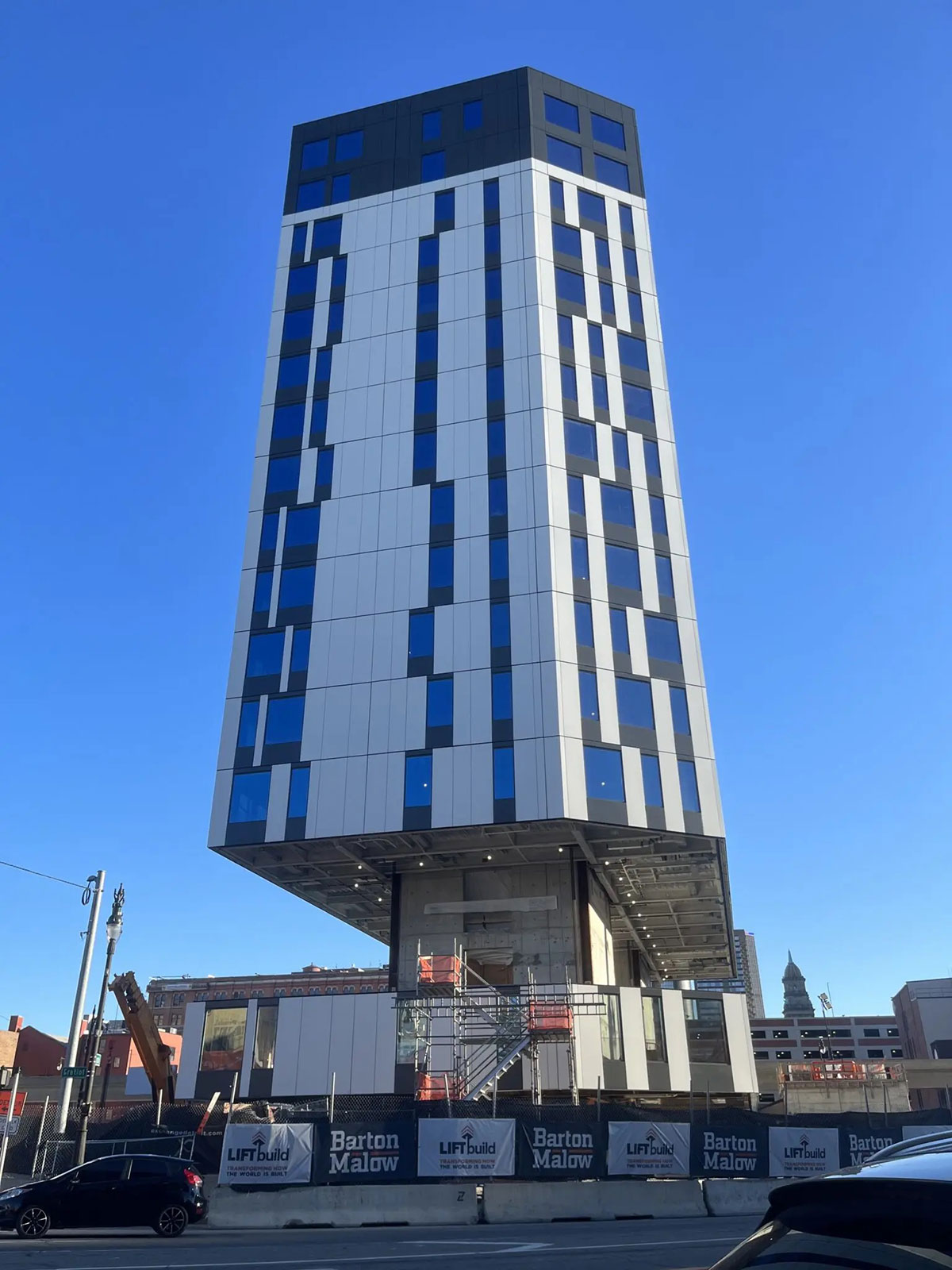
On 19 January, LIFTBuild announced the successful application of an experimental technique in the prefabricated modular construction of a new residential development. The popular Spanish expression "to build a house from the roof down" perfectly illustrates the new technique applied by LIFTBuild in the construction of the Exchange Building in the Greektown neighbourhood of Detroit, USA. This experimental technique had a precedent in the so-called Youtz-Slick (or Lift Slab Construction) method, which involves stacking floor slabs of different heights of a concrete building and lifting them one by one, with huge hydraulic jacks, into their final position. LIFTBuild's parent company, Barton Marlow, led and financed a scheme that it says served as a "prototype project" to demonstrate the viability of the new building concept. But let's look at how LIFTBuild carried out the construction of the Exchange Building.
First, two "concrete structural spines" were erected on top of the foundations, up to the full height of the building, with the staircases and lifts housed inside. Once the foundations and the spines or cores of the building were in place, the crown of the building was built around them on the ground. So, on 30th April 2021, the crown began to rise from the ground along the cores at a speed of 6 m/h, and 10 hours later it reached its final position at the top of the building. From then on, each floor was built in the same way, on the ground and around the two cores.
First the floor (or roof of the next floor) was built with steel and concrete, then the walls and enclosures, electrical and plumbing, fire protection, ducts and finally the partial façade. For the installations in the lower part of the floor, all that was needed was to raise the floor to a comfortable working position. Once completed, the 500 tonnes of plant were lifted with the aid of eight powerful jacks and cables into their final position on the building's upper levels. This is how LIFTBuild proceeded until, nine months later, it completed the construction of the last of the floors, which in this case remained one of the first in the building. It was the fourteenth in order of construction, although in reality it was the third of the Exchange Building's 16 floors, since the first two floors, which are used for offices and commercial space, are built according to the traditional method.
As a consequence of this experimental construction technique, each floor, supported only by its connection to the two central cores, represents an open-plan space, with no trusses, columns, structural supports or walls. In this way, each floor is like a blank canvas on which the architect can determine the design and layout of the space at their own discretion.
The advantages of this new prefabricated modular construction method include simplification and standardisation, thereby improving process efficiency and potentially saving time and budget. At the same time, it provides a safer and more productive working environment than conventional construction, as it eliminates work at height and the need for tower cranes and additional equipment. Similarly, the technique reduces the possibility of falls, the main cause of serious or fatal accidents in the construction industry. To summarise, LIFTBuild chief operating officer Joe Benvenuto said: "the implementation of our proprietary methods has now been proven to produce the advantages we were anticipating, and we are confident that the results achieved at the Exchange Building will set the stage for a broader commercialization of LIFTbuild'.
You can check all this out in this short VIDEO
Sources: LIFTBuild, Barton Maslow, New Atlas, Wikipedia. Images: LIFTBuild y Barton Marlow.