In leisure and tourism projects, and especially in theme parks, theming produces unique spaces with the objective of integrating them into a narrative that transports visitors and tourists to imaginary, historical, cultural, futuristic, natural worlds… But to achieve this objective with an unquestionable degree of quality, the theming process must resort to artistic and technical skills, in addition to having sufficient manufacturing capacity. These artistic and technical skills include the following:
-Reproductions in plaster.
–Fibreglass reproductions using moulds.
–Fibreglass reinforced concrete (GRC) formwork formwork.
–Sprayed mortars, sculpted in-situ.
–Hand carving of wood, stone or other natural materials.
-Shaping of metal sheets.
–Digital printing with different materials.
–Three-dimensional modelling of expanded polystyrene (or EPS).
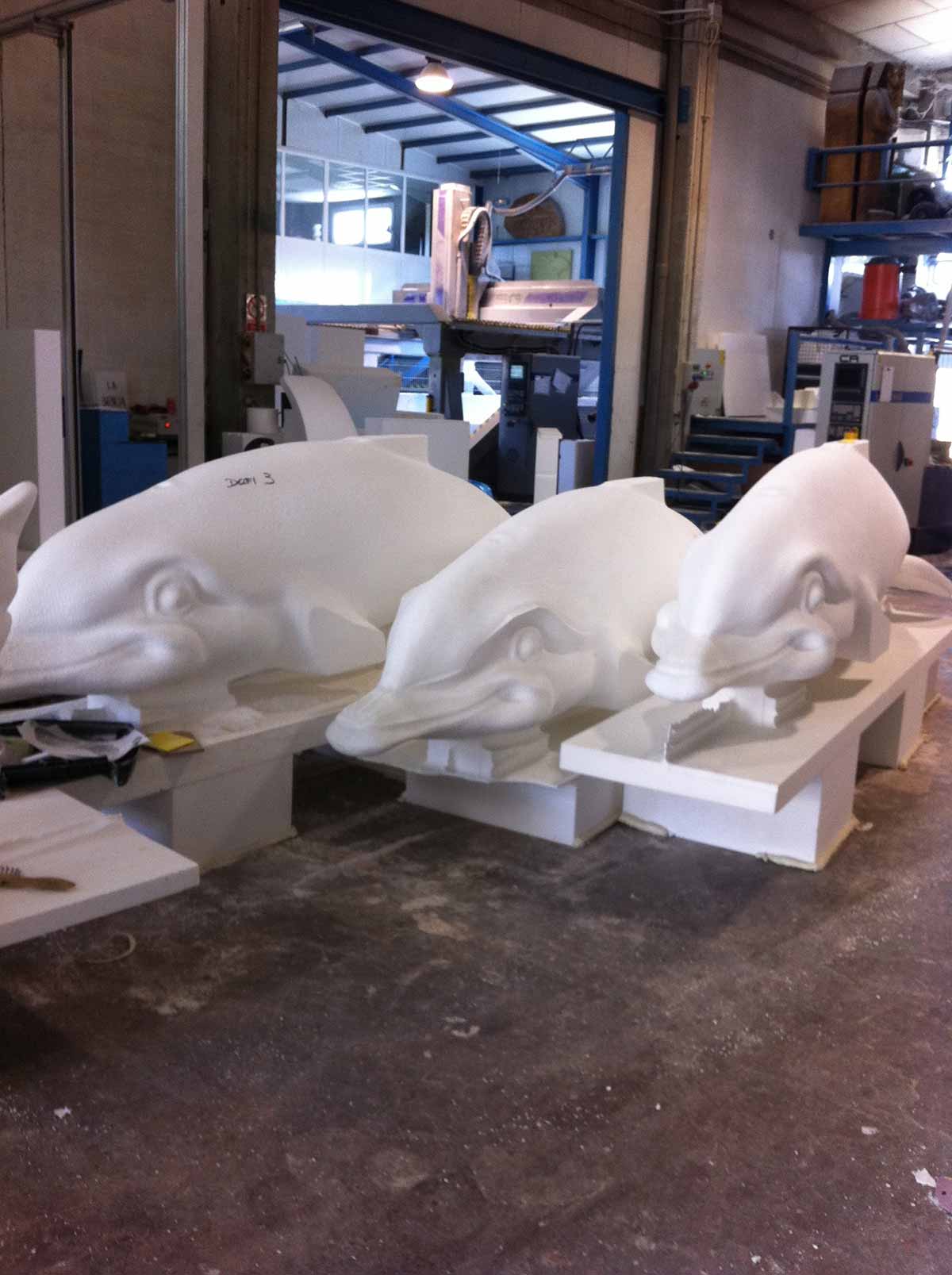
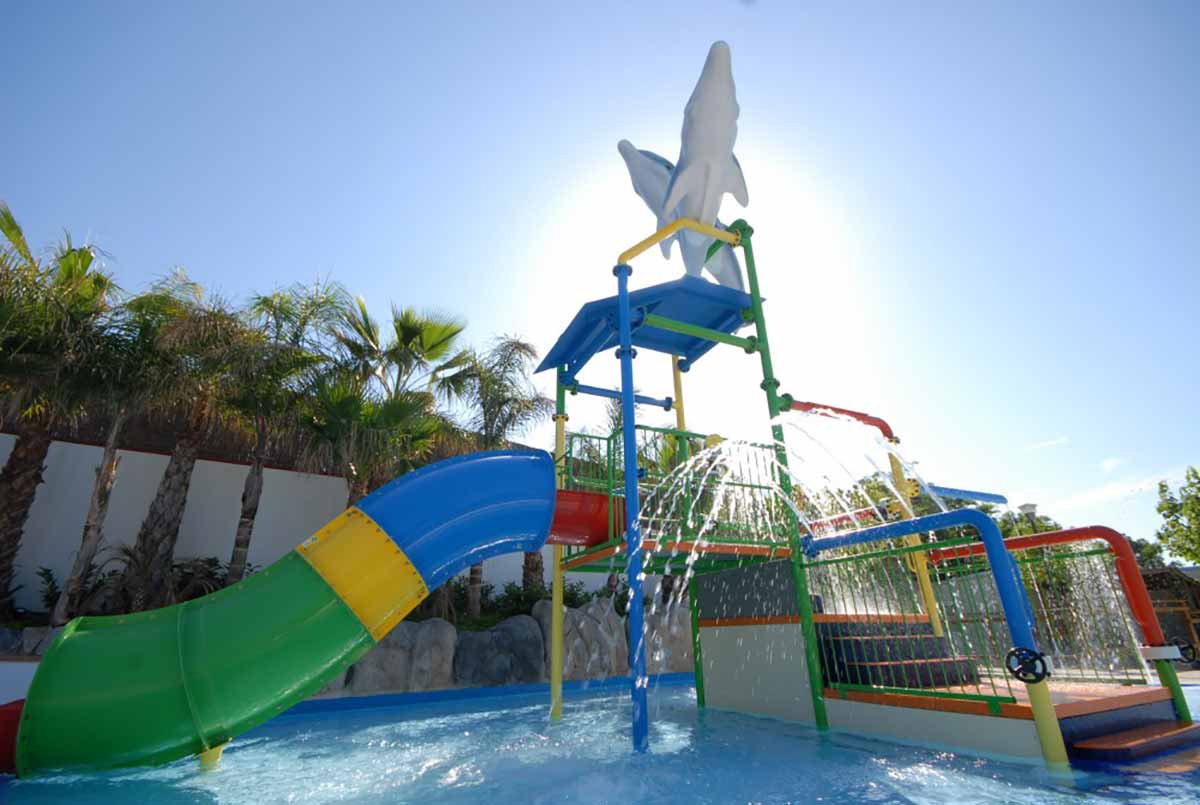
Let us look at the advantages of the latter process, that of three-dimensional modelling of figures in EPS.
EPS is a three-dimensional material, in large blocks, from which specific geometries are obtained, depending on each project. Its lightness and ease of transport make it suitable for the prefabrication of thematic elements and their subsequent assembly and installation on site.
The technology currently used for the development of leisure and tourism projects such as theme parks is the BIM (or Building Information Modelling) methodology.
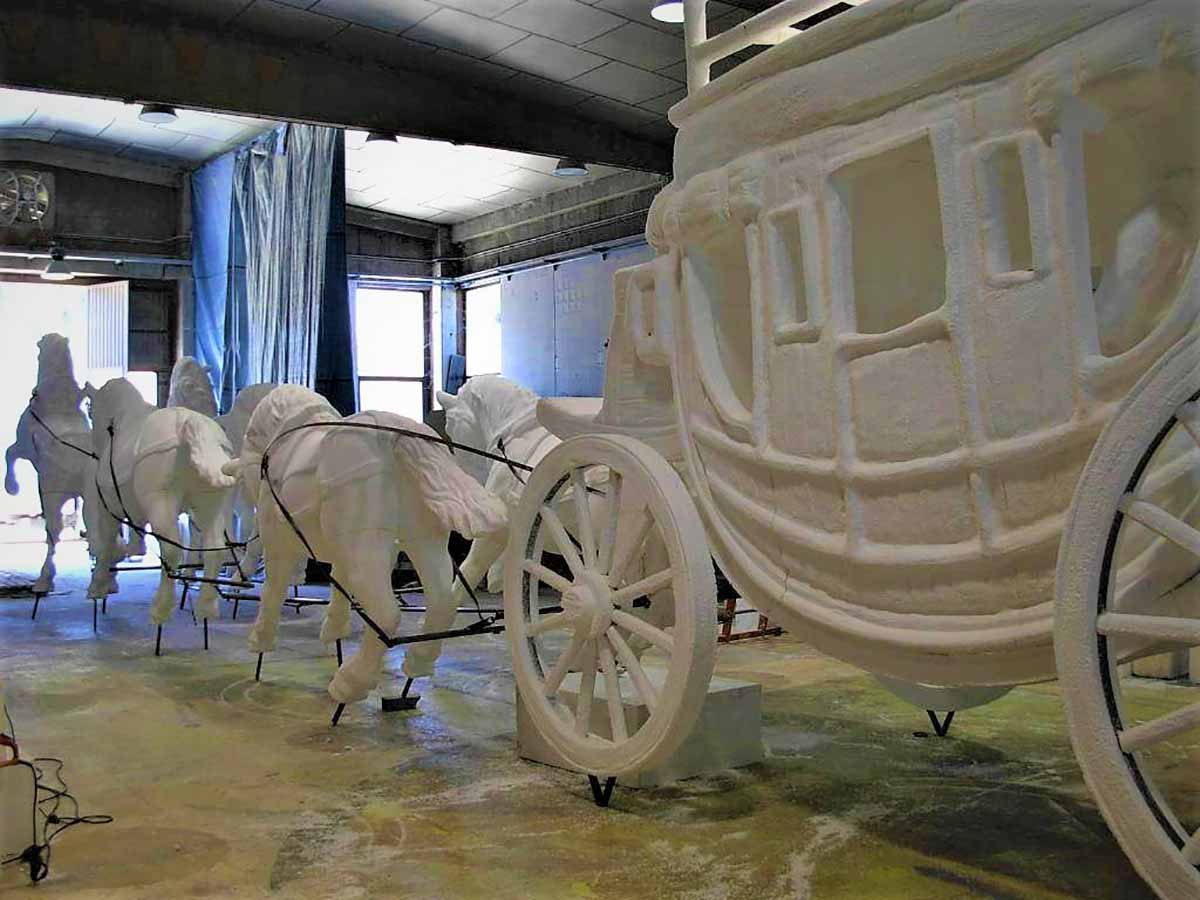
After all, the machining and sculpting (or milling) of EPS blocks requires a three-dimensional model. This makes it possible to coordinate the design and manufacture of thematic elements with the three-dimensional models of the building and its architecture and thus to achieve maximum precision in the process. Finally, the BIM model of the project, which includes all other disciplines, allows:
-The detection of collisions with structural elements.
-Foreseeing openings or apertures for the passage of installations, ducts and wiring.
-Consideration of the location of other elements of furniture, signage, lighting or decoration that are integrated with the thematic elements.
-Establishing anchorage and support points for the secondary structure of the thematic element on the main structure of the building.

From the three-dimensional digital model, milling (or sculpting) is carried out using specialised techniques such as hot wire cutting and CNC milling. To ensure the durability and appearance of the manufactured themed elements, a variety of specialised coatings are used to provide the performance required for the project.
The use of these manufacturing techniques, especially for one-off parts and reproductions, makes it possible to dispense with moulds and therefore reduce costs. At the same time, the use of robots means that identical parts can be produced in series without the need for specific moulds.
However, the following are some of the theming elements that we manufacture using these techniques:
-Three-dimensional corporeal figures in different scales and sizes that recreate characters from the narrative of the particular theme park project.
-Three-dimensional figures for branding and corporate events.
–Sculptural elements for public parks, exhibitions, museums or for educational purposes.
-Decorations for façades (or complete facades).
-Decorations for interior design.
–Signage elements and backdrops for photography (known as photocalls).
–Scenery for films, theatres and TV commercials.
–Decorations, elements and objects for interactive experiences, such as in escape games (or what are commonly known as “escape rooms”).
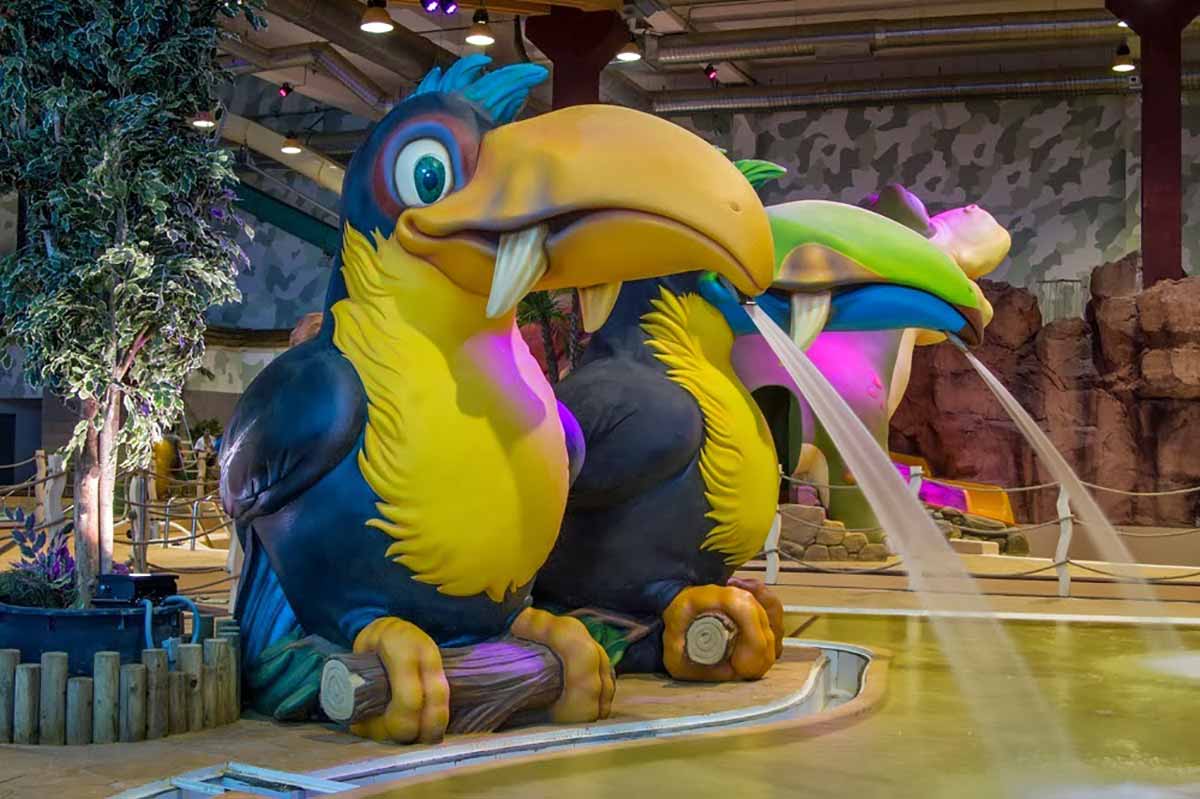
Amusement Logic has extensive experience in the use of these techniques, which it applies in a personalised way, specifically for each theme park project, or any other project aimed at leisure and tourism.
By Cristina Uchán, senior architect in Amusement Logic’s Architecture Department.
RELATED STORIES
Newsletter