Galvanising is a technique that has been used for over 250 years to protect metals from corrosion. It dates back to the research of the physician Luigi Galvani (1737-1798). He discovered that when a sectioned frog’s leg is placed in contact with metal, it contracts as if it were alive. After experimenting with different metals, Galvani found that the frog’s leg reacted to different degrees. He discovered that each of them has a specific electrical charge.
Subsequently, Galvani observed that a metal with a higher charge will coat a metal with a lower charge, a key principle for the development of the electroplating process we know today. The main function of galvanising is to protect the surface of a metal against oxidation, a natural process by which metals return to their original mineral state when exposed to the environment.
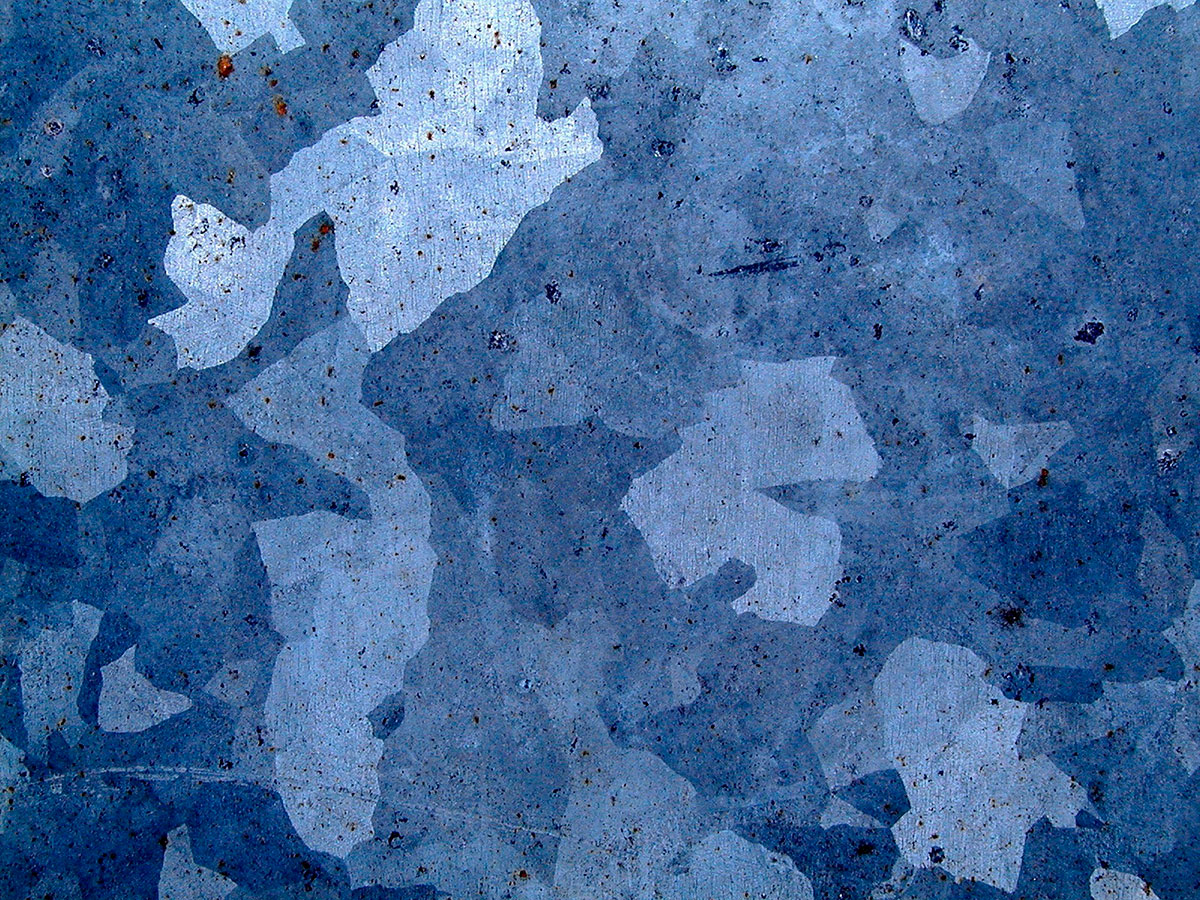
Applied to structural steel, galvanising involves coating the surface of the metal with zinc (Zn), which not only prevents corrosion, but also increases the mechanical resistance of the material to impact and abrasion. The two most common techniques are hot-dip galvanising and cold galvanising, each of which is regulated by specific standards and used according to the purpose of the material.
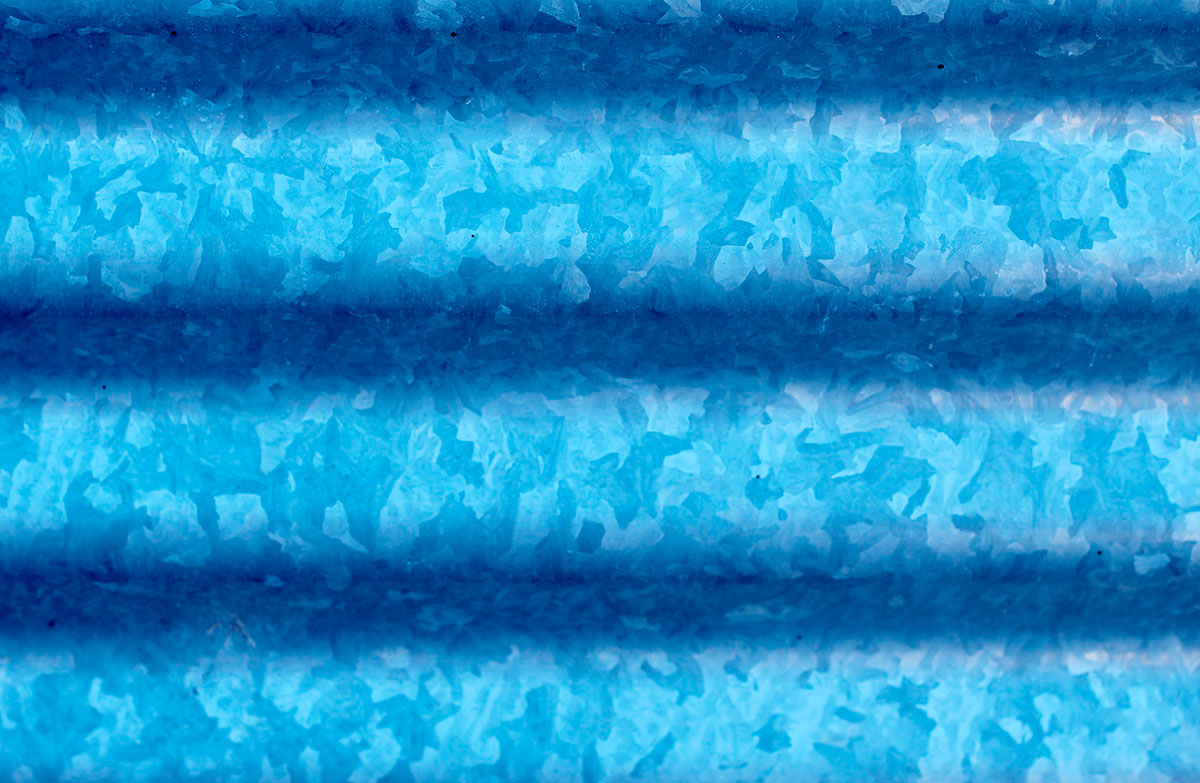
Hot-dip galvanising technique
This process consists of immersing steel parts in molten zinc at approximately 450°C. The resulting coating can vary between 2 and 200 microns. The environment in which the steel will be used determines which coating is used. The UNE EN ISO 10346 or UNE EN ISO 1461 standards regulate the type of coating depending on whether low or high durability protection is required.
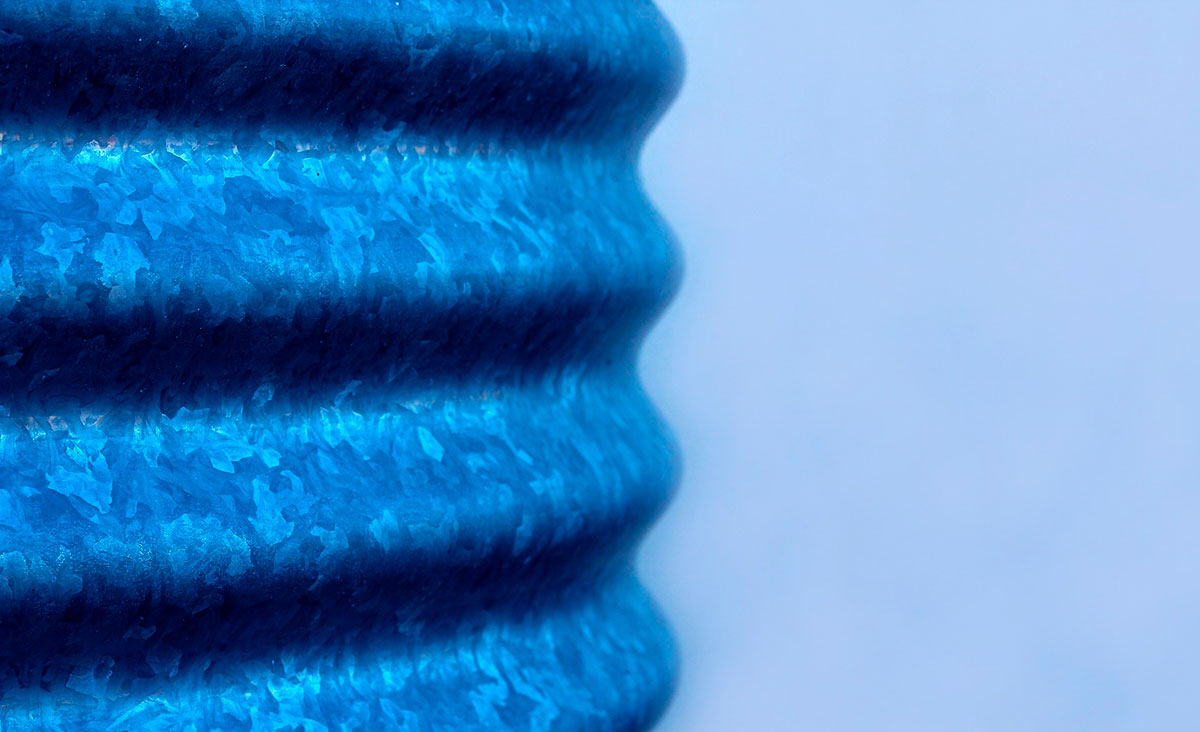
Cold galvanising technique
In this case, zinc powder is applied to the surface of the steel by painting. Although its cathodic protection and service life are less than those of hot-dip galvanising, it is still an effective option in certain cases. The effectiveness of this technique, regulated by the ISO 8501.1 standard, is based on the coating containing at least 95% zinc and being sufficiently conductive to protect the metal.
Applications and advantages of galvanising
Galvanising offers numerous advantages, including increased strength, service life and conductivity of metal parts, especially structural steel. This material is one of the most widely used in buildings, water parks and theme parks.
Today, galvanising is also used in metal finishes for aesthetic purposes, whether on consumer products, sculptures, figures or works of art. Manufacturers opt for this technique to create lighter and more easily transportable parts, often with substrates that reduce shipping and handling costs.
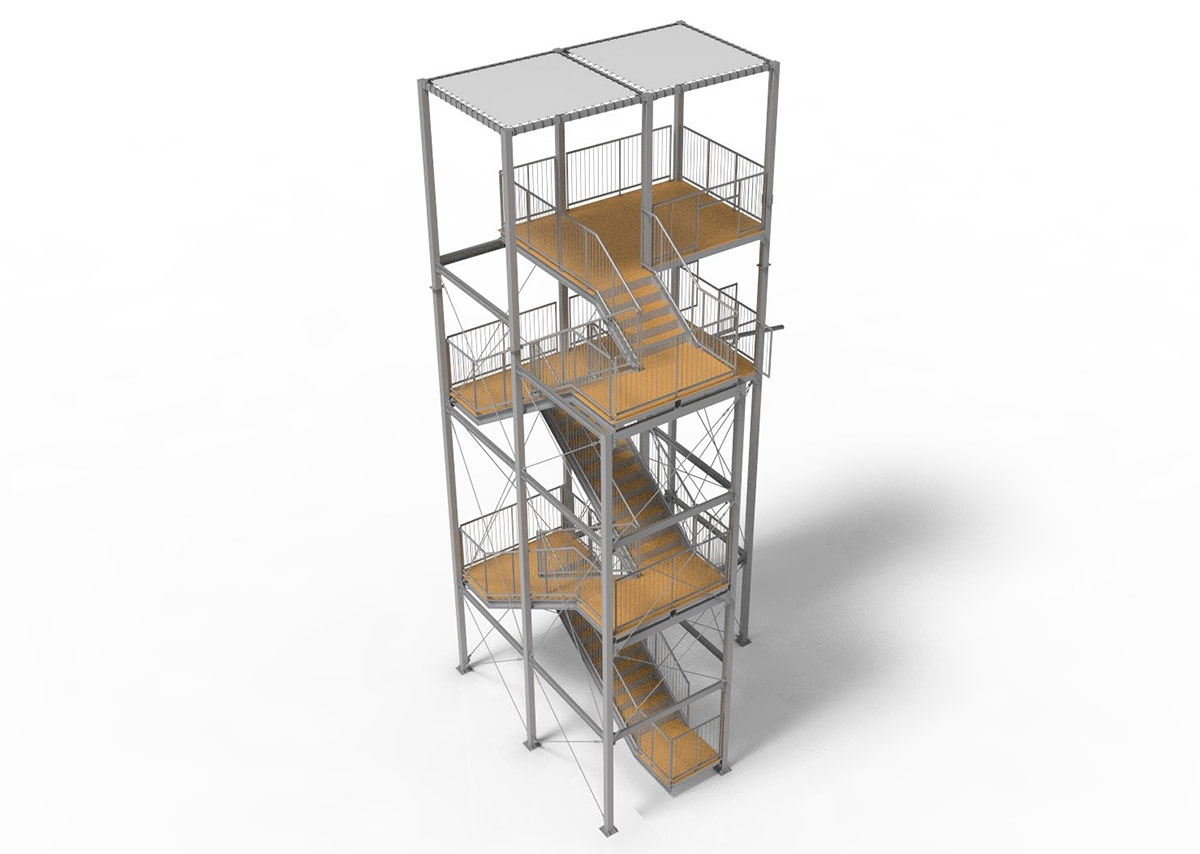
By Jean Carlos Soto, Senior Structural Engineer in Amusement Logic’s Architecture Dept.