Since the first tests in the late 1980s, fibreglass reinforced polymer (GFRP) rebars have evolved to become a particularly relevant technical solution in construction projects where corrosion of conventional steel represents a critical challenge. Their adoption has accelerated since 2000 in aquatic or aggressive environments, where durability and corrosion resistance are priorities.
Technical characteristics and comparison with steel
Its main advantage over conventional steel lies in its complete immunity to corrosion, even in marine environments, or those with a high presence of chlorine. Furthermore, they are up to 75% lighter, making them easier to transport and handle on site. Another key property is their non-conductive nature, both electrically and magnetically, expanding their applications in specialized installations.
However, GFRP rebars have limitations that require specific design. Its lower elastic modulus can translate into greater deformations under load, while its brittle behaviour—unlike the ductility of steel—requires careful consideration of failure mechanisms.
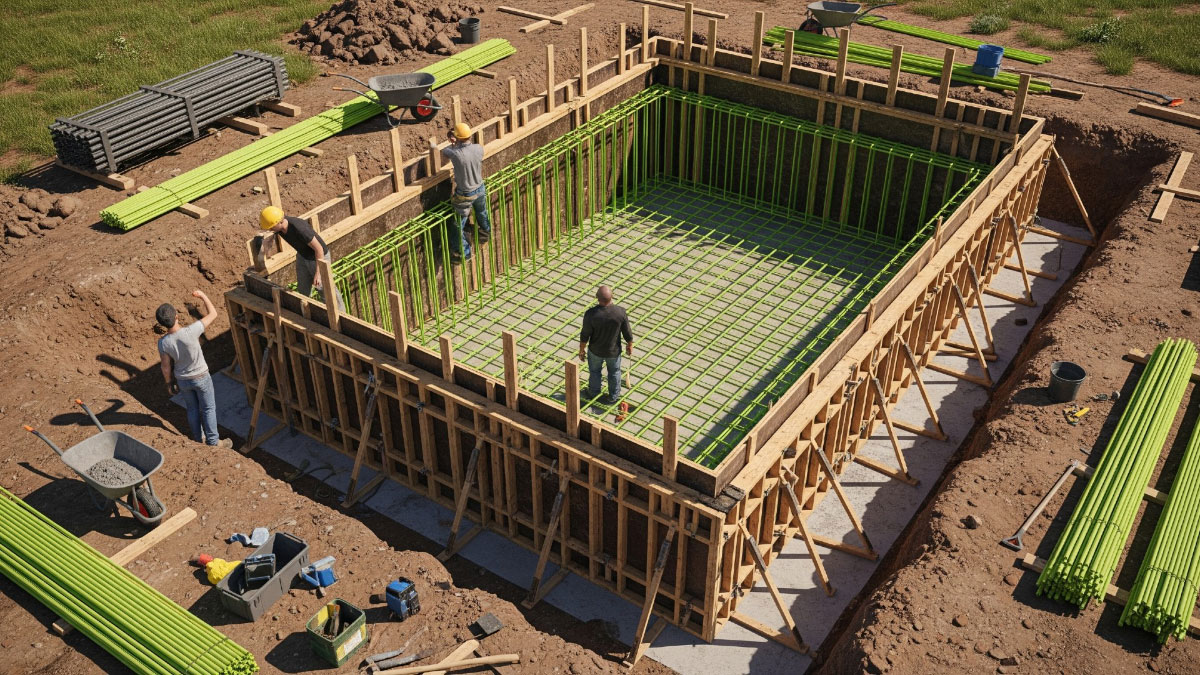
Practical Applications in Europe
In the Netherlands, for example, GFRP has been used to eliminate the problem of rust in bridges and port structures exposed to saltwater. Switzerland has applied these bars in underground tunnels, where constant humidity compromised the steel. Projects in Germany and the United Kingdom, on the other hand, leverage its lightness to reduce structural loads in tall buildings without sacrificing strength.
Suitability for Swimming Pools and Hydraulic Structures
GFRP’s resistance to corrosive agents such as chlorine, thermal changes, and constant humidity make it ideal for swimming pool structures. Its lightness, on the other hand, facilitates its construction, while its non-conductive nature adds safety to public swimming pools.
However, for the implementation of GFRP in construction, the design must consider its lower rigidity and, consequently, greater vulnerability to deformation. Of course, it is essential to verify its compatibility with local building regulations. Although the initial investment is higher, the reduction in maintenance costs and the extension of its service life justify its use in construction projects with long time-horizons.
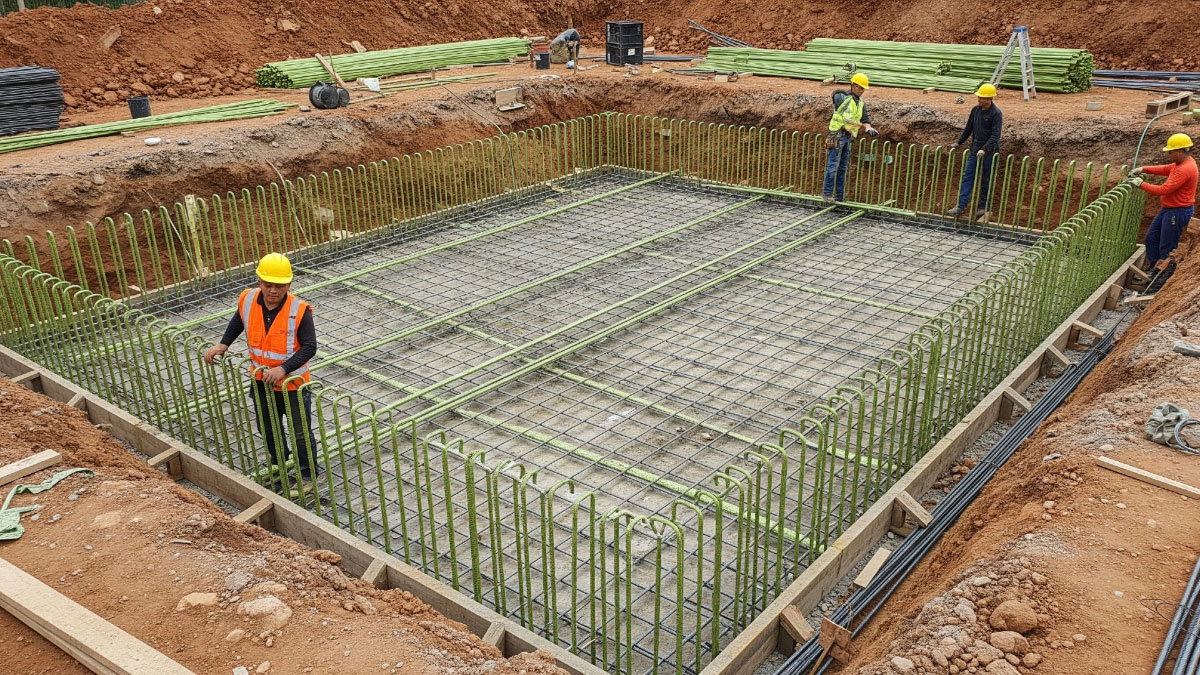
Future prospects and sustainability
For all the above reasons, and due to its low environmental impact—by avoiding the carbon-intensive processes associated with steel—the adoption of GFRP in construction benefits from the push by European policies for the use of sustainable materials. As specific regulations are developed and production costs are optimized, its presence in the construction sector will expand.
By Ángel Ibáñez Pérez, Senior MEP Engineer in the Architecture Department at Amusement Logic