The rise of industrialised construction and, with it, the execution of works using “dry construction” techniques, brings with it an increase in the use of one of these techniques. This is known in the sector as Steel Framing. It consists of a technique based on the use of cold-formed, structural grade galvanised steel, using C-shaped profiles and U-channels, joined by means of self-drilling screws. This construction technique originated in the United States, from where it spread to Canada and other countries in the Americas.
The Steel Framing technique offers advantages over conventional construction. The lighter weight of the structures compared to those built with concrete, or the improved efficiency thanks to standardisation and mass production, or the reduction of pathologies derived from the wet construction site, or its suitability for any climate, are some of these advantages.
The assembly of Steel Framing profiles forms a three-dimensional framework or frame that encloses the main volumes of the building. These frames are clad with interior and exterior materials such as OSB (Oriented Strand Board), plasterboard, vapour barriers, thermal insulation and various types of panelling, all in dry construction.
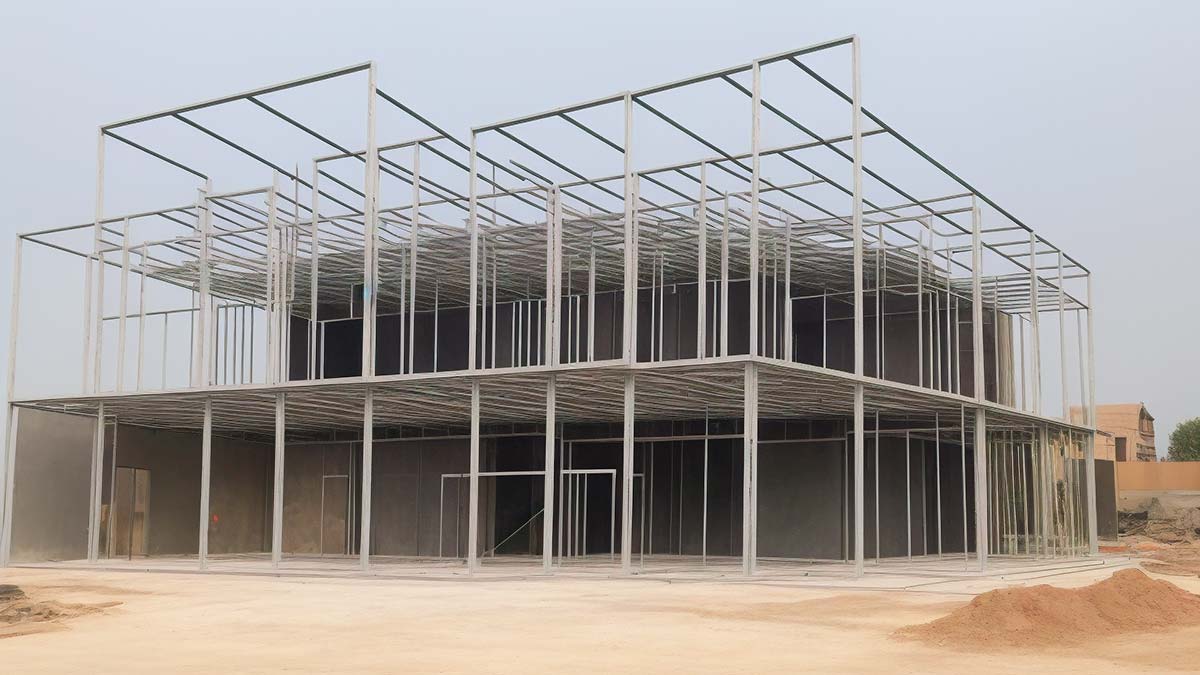
There are many options on the market for façade finishes that meet the aesthetic and architectural requirements of Steel Framing. One option is prefabricated EPS (Expanded Polystyrene) modules, cut in the factory according to the shapes and needs of the project and coated with specific cement mortars for external thermal insulation systems.
This combination of systems offers thermal and aesthetic solutions, in a single lightweight, prefabricated and customised element, with numerous advantages. In addition to those already mentioned, the dry execution of this technique entails speed and cleanliness, aspects synonymous with sustainability and low costs nowadays.
By Pablo Vidal, senior architect in Amusement Logic’s Architecture Department.